Základním požadavkem po rekonstrukci Barrandovského mostu je zvýšit jeho zatížitelnost. Aby bylo dosaženo vyšší zatížitelnosti, je nutné provést dodatečné podélné předpětí nosné konstrukce mostu, které doplní stávající předepnutí. Na základě výpočtového modelu vychází i rozdílné reakce na stávající hrncová ložiska.
Na Barrandovském mostě byly osazeny tři standardní druhy hrncových ložisek – pevná, podélně vedená a všesměrná. Nosná konstrukce levého mostu byla osazena na 22 kusech hrncových ložisek a nosná konstrukce pravého mostu byla uložena na 17 kusech hrncových ložisek. Hrncová ložiska byla vyrobena v bývalé NDR ve výrobním závodě v Bernsdorfu. Vzhledem k době výstavby obou (levý a pravý) mostů byly použity dva vývojové typy hrncových ložisek.
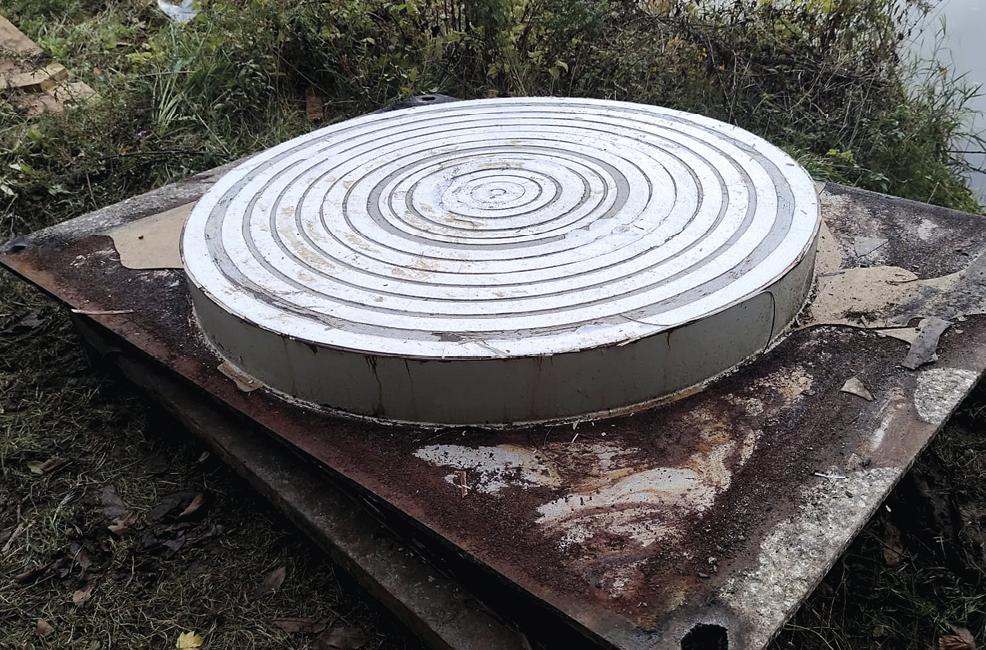
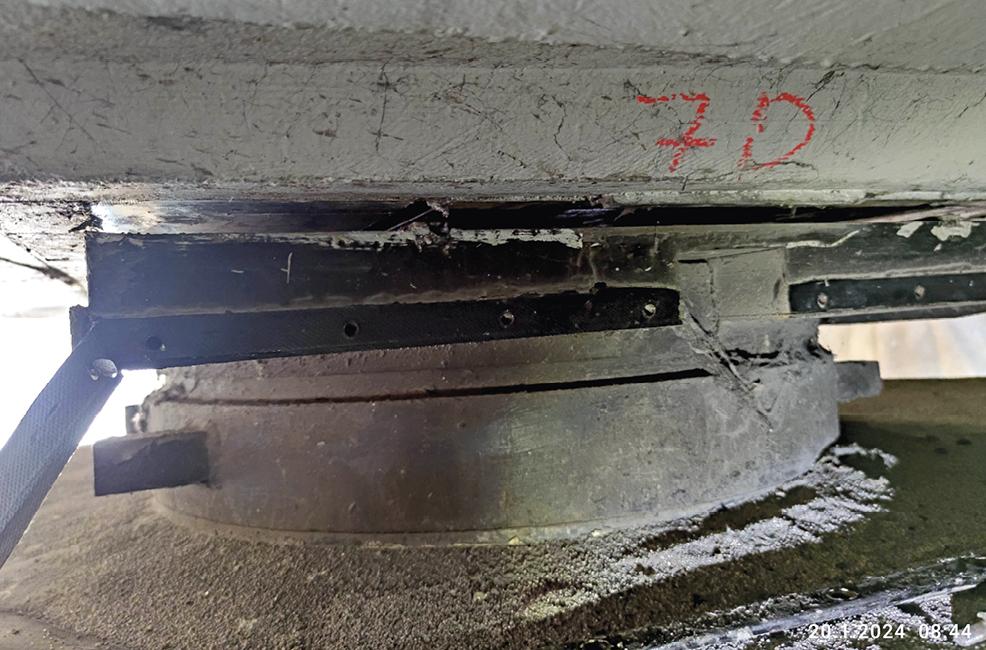
První typ (starší) ložisek GTL byl vyroben podle oborové normy TGL 18 204 (NDR) Blatt 2–8/68. Elastomerová vložka je umístěna pod konstrukcí hrnce, následně je osazen vlastní hrnec a kluzná deska opatřená pertinaxem, která je uzavřená v ocelové obálce ložiska. Tento typ ložisek neumožňoval provedení jakékoli kontroly kyvné spáry, kluzné spáry a stavu vnitřního kluzného materiálu.
Druhý typ (novější) ložisek GTL byl vyroben podle oborové normy TGL 18 204 (NDR) č. 2–1/83. Zde už se jedná o standardní hrncová ložiska, kdy na hrnec je položeno víko a je osazen kluzný teflonový materiál. U tohoto typu ložisek je možné již provádět kontrolu kluzné a kyvné spáry, potažmo vnitřního kluzného materiálu.
S ohledem na stáří, životnost a nosnost hrncových ložisek byla navržena jejich kompletní výměna za nová kalotová ložiska s minimální životností 50 let. Nová kalotová ložiska byla vyrobena v závodě firmy Maurer SE v Mnichově.
S ohledem na velmi složitý tvar mostu při výpočtech metodou konečných prvků vznikla tahová reakce v tupém rohu na opěře 1 – ložisko 1e (levý most). U novostaveb lze provést nová ložiska i jako tahová. U rekonstrukcí by bylo nutné provést kotvení do nosné konstrukce a spodní stavby s ohledem na zachycení tahových sil, což by v tomto případě představovalo téměř neřešitelný problém. Projektant mostu navrhl řešení, které eliminuje tahovou reakci u ložiska 1e. Řešení spočívá ve výškové rektifikaci nosné konstrukce v ose ložisek po celé délce opěry 1 levého mostu, než bude uložena na nová kalotová ložiska.
Pro ověření předpokladu výpočtu, zjištění přesných reakcí na jednotlivá ložiska a přesné provádění výškové rektifikace byl navržen speciální systém zvedání. Základním požadavkem systému zvedání nosné konstrukce bylo zjištění přesné výšky zdvihu (s přesností na setinu milimetru) a reakce (kN) v reálném čase na pěti místech současně. Na základě dlouhodobé spolupráce firmy Cirmon s.r.o. a firmy Třeštík s.r.o. byl vyvinut a aplikován systém synchronního zvedání v reálném čase a s přímým digitálním záznamem.
Hydraulické zdvihací lisy byly umístěny u stávajících ložisek dle předem daného a odsouhlaseného schématu projektantem mostu. Tyto lisy (u každého jednotlivého ložiska) byly napojeny na samostatný hydraulický okruh. Celkem tedy bylo použito pět samostatných hydraulických okruhů. Do každého jednotlivého okruhu byl v místě blízkosti lisů osazen digitální nanometr. U stávajícího ložiska byl osazen digitální úchylkoměr s přesností měření na jednu setinu milimetru.
Nanometr a úchylkoměr z každého ložiska byl zapojen do sběrnice dat, která data přenáší do PC. V PC je zobrazena hodnota tlaku v každém hydraulickém okruhu, hodnota z úchylkoměru a proveden automatický výpočet reakce u jednotlivého ložiska a celkové reakce pro všechna ložiska na opěře 1. Dále je automaticky ukládán záznam z průběhu zvedání v časovém intervalu 5 sec. pro zpětnou kontrolu a následné vyhodnocení zdvihu nosné konstrukce mostu.
Díky tomuto inovativnímu přístupu ke zvedání mostu bylo značně usnadněno porovnání předpokladu výpočtu a skutečné reakce mostu. Systém monitoringu byl nakonec použit při každém zvedání na Barrandovském mostě – na všechna měněná ložiska na všech opěrách a pilířích mostu.
Na závěr bychom chtěli poděkovat jmenovitě panu inženýru Milanu Šístkovi za projevené úsilí a angažovanost při individuálním řešení zdvihu každé opěry a každého pilíře Barrandovského mostu.
Autoři:
Ing. Eduard Cirmon, Cirmon s.r.o.
Ing. David Knoll, Cirmon s.r.o.